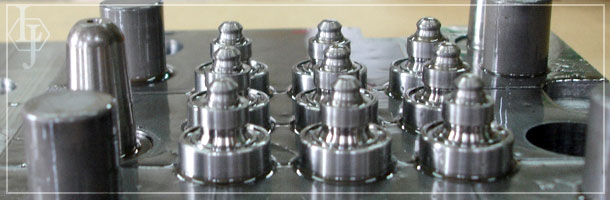
Rubber Mold - Plate
Plate mold is machining cavity directly on mold steel plate or making cavity separately then "insert" it into mold steel plate so the cavity becomes replaceable.
Comparing with cavity mold, the main advantage of using plate mold is to reduce the unit cost of mass production. However, how to control molding pressure with other production parameters well is a technical topic to be dealt with.
On the other hand, you must consider how plate mold coordinates with your machine in working action, heating plate size, pressure output, daylight, stroke, mold fixture, and so on. Those conditions should be coordinated through well communication.
Anyway, rubber plate mold is usually used for making standard & customized rubber component parts. Basically speaking, it has 3 kinds of method which are: Compression, Transfer injection, and Injection molding process.
The selection of what mold type is a professional topic and the first question you have to consider. L&J usually analyses the limitation of mold design, and advantage & weakness of mold type selection from product quality, rubber machine, operating way, and production cost point of view to customer's reference. Customers may also need further suggestions on mold material, mold design, compound rubber, chromate plating, or any other kinds of technical question so L&J would be a very good consultant on those demands.
Doing mold test is also a critical process in mold development. Sometimes a mold maker is not really familiar with mass production conditions and requirements so needs the opinions from professional manufacturing factory to improve mold performance. The risk is, during the mold-test process, the mold supplier cannot distinguish what problem is from mold, what problem is from molding conditions (parameter) in production. L&J has strong resources to integrate the know-how of mass production and mold-making together which makes mold test become more professional to solve problem. Usually this feature is not able to be done from other mold suppliers.
Buying mold from L&J, you don't need to worry about the risk of what if fail unless you cannot clearly explain the materials required for making this mold. We will estimate risk during quotation stage in advance. When we accept your purchase order, it means that we will be responsible to finish this order completely. Even after you approve and receive our molds, we will be pretty serious to do after-sales service well through providing consulting and any possible supports which we are able to do, because selling molds is not just selling, it is also a duty to make sure mold running well.
For more information in detail, please make contact with us.
This is the wooden packing to rubber plate mold with good antirust treatment which is safe for shipment:
Compression Mold
Compression molding process is directly arranging rubber strip above cavity then close mold...
DetailsTransfer Injection Mold
Transfer injection molding process is arranging rubber strip on a chamfer mold plate, then...
DetailsInjection Mold
Injection molding process is using rubber injection machine to inject rubber compound into...
DetailsHow do you determine which rubber mold type is right for your production requirements?
Selecting between compression, transfer injection, or injection molding processes requires careful analysis of your production volume, part complexity, and quality requirements. L&J's technical team conducts comprehensive assessments of your specific manufacturing conditions, including machine specifications, operating methods, and cost considerations to recommend the optimal mold solution. Contact us for a professional consultation to maximize your production efficiency and product quality.
Our professional team guides customers through the entire mold development process, from initial design analysis to mold testing and implementation. Unlike standard mold suppliers, L&J integrates mass production know-how with expert mold-making capabilities, effectively troubleshooting issues during testing phases to optimize mold performance. We offer three distinct molding processes—Compression, Transfer Injection, and Injection—each tailored to specific production requirements, alongside exceptional after-sales support and consultation services to ensure long-term operational success.